Cargo bikes are no longer confined to traditional cargo and delivery applications; they are diversifying into personal use, family transportation, and more. Through unique and flexible assembly solutions, manufacturers can increase production capacity and quality control ensuring sustainable growth and adapting to future demand. This is where Overhead Conveyor Systems (OCS) comes in, helping leading bicycle manufacturers improve their business and profitability through custom-made kitting and assembly solutions.
Bike assembly challenge
Designing assembly lines presents a challenge; how to optimize production flow considering the diverse mix of different bicycle types, from road bikes to cargo bike, with varying assembly times. Cargo bikes come in various sizes and configurations, making assembly a complex task. Ensuring that the right components are seamlessly integrated into each cargo bike, regardless of its specific design, requires a well-thought-out assembly process. In the end, it’s about maximizing operator efficiency by reducing wastes such as waiting times and other non-value-added activities.
Operators can walk freely around the ergonomic workstations and the bike can be turned 360°”
Efficiency and profitability
With extensive experience in designing assembly lines across various industries, including the European bicycle industry and the global Automotive industry, OCS emerges as a vital partner. The expertise in designing optimal bicycle assembly solutions to minimize bottlenecks, reduce material handling and ensure smooth workflow, aligns perfectly with manufacturers’ production goals. By collaborating closely with bicycle manufacturers to understand their unique needs and requirements, including production capacity, component diversity, and workflow, OCS creates customized bike assembly solutions, hanging from above, that enhances operational efficiency.
The overhead conveyor systems are engineered for efficiency, adept at handling the weight and bulk of cargo bike components, ensuring a smooth and seamless assembly process.
Space optimization
Transformation from traditional floor-based assembly to an automated hanging solution have drastic effect on production capacity and output. The overhead conveyor frees up valuable floor space, creating improved working conditions for operators. The assembly team can work around the bikes in various angles. Operators can walk freely around the ergonomic workstations and the bike can be turned 360°, which means ideal working conditions for the assembly team.
Component handling made easy
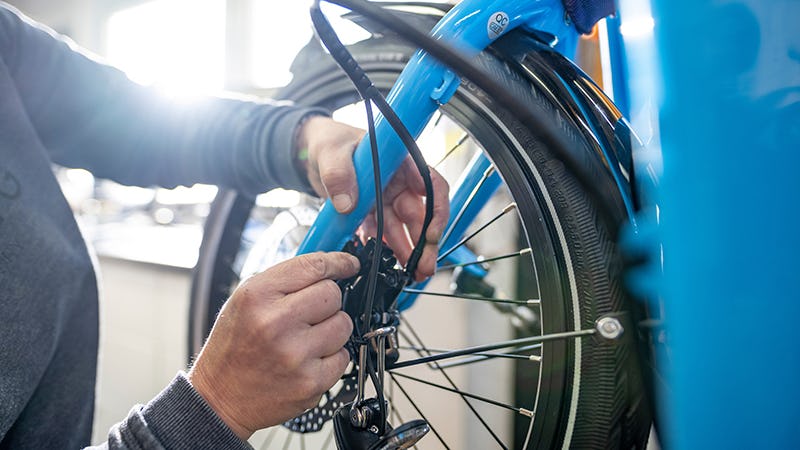
Efficient handling of wheels and frames, integral components of cargo bikes, is simplified through smart overhead storage solutions. Pairs of wheels and frames can be stored together, delivered to the right assembly station in the correct sequence, and at the right time. This solution ensures precision in storage, delivery, and assembly, keeping cargo bike production on track and highly productive.
The conveyor technology
The conveyor technology offers friction-driven, low-noise, oil-free, and clean overhead conveyors that are modular and highly flexible to meet future demand. They allow full line accessibility for operators and smart layout and line design to optimize floor space utilization. Custom-made carriers provide full 360° bicycle accessibility, height adjustability, and specialized features for component and wheel storage, ensuring efficient and precise assembly. These innovative solutions offer a comprehensive approach to enhancing cargo bike production, supported by OCS's expertise and experience.
Investing in the correct assembly solution and optimal line design, prioritizing operator efficiency and ergonomics, can yield increased production capacity while simultaneously reducing costs associated with kitting and assembly processes.
This article is sponsored by OCS Overhead Conveyor.