The factory operates on an innovative model acquired from the automotive industry, according to the standards established in World Class Manufacturing (WCM). The production process is built according to the one-piece flow method. By balancing the production lines, increased efficiency is achieved, limiting operational stock, as well as reducing production waste, through fully integrated quality monitoring in the production lines.
Production lines are the latest generation, ergonomic, developed to support the work of all operators. The assembly stations are gathered closely and operate just on time. From the tires, handlebar and fenders to the assembly of the wheels, the operations are fully synchronised, and at the end of the line a fully packed electric bicycle is ready for dispatch.

Focus on optimisation and quality
The Europe-wide breakthrough of the e-bikes in the past years accelerated the trends for more production efficiency and the global trend of Industry 4.0 production. Following the growing demand, Leader 96 focuses its production on e-bikes and aims higher: to become a name in high-end e-mobility business through modernisation, effective supply chain management and strict quality control to cover the requirements of the ever-growing number of customers.
The company increases the investments budgets creating room for production automation on a level the bicycle industry has not experienced before. In combination with the bigger complexity of the high-end e-bikes, this makes it possible to create more quality control during the various stages in production.
While regular bicycle assembly only provides quality control at the end of the line before packaging, this no longer meets today’s standards. Leader implements quality control at the end of each step in the flow. This is in line with a system of various quality levels known from the automotive industry. Production and tooling automation allow for this important step to improve quality control.
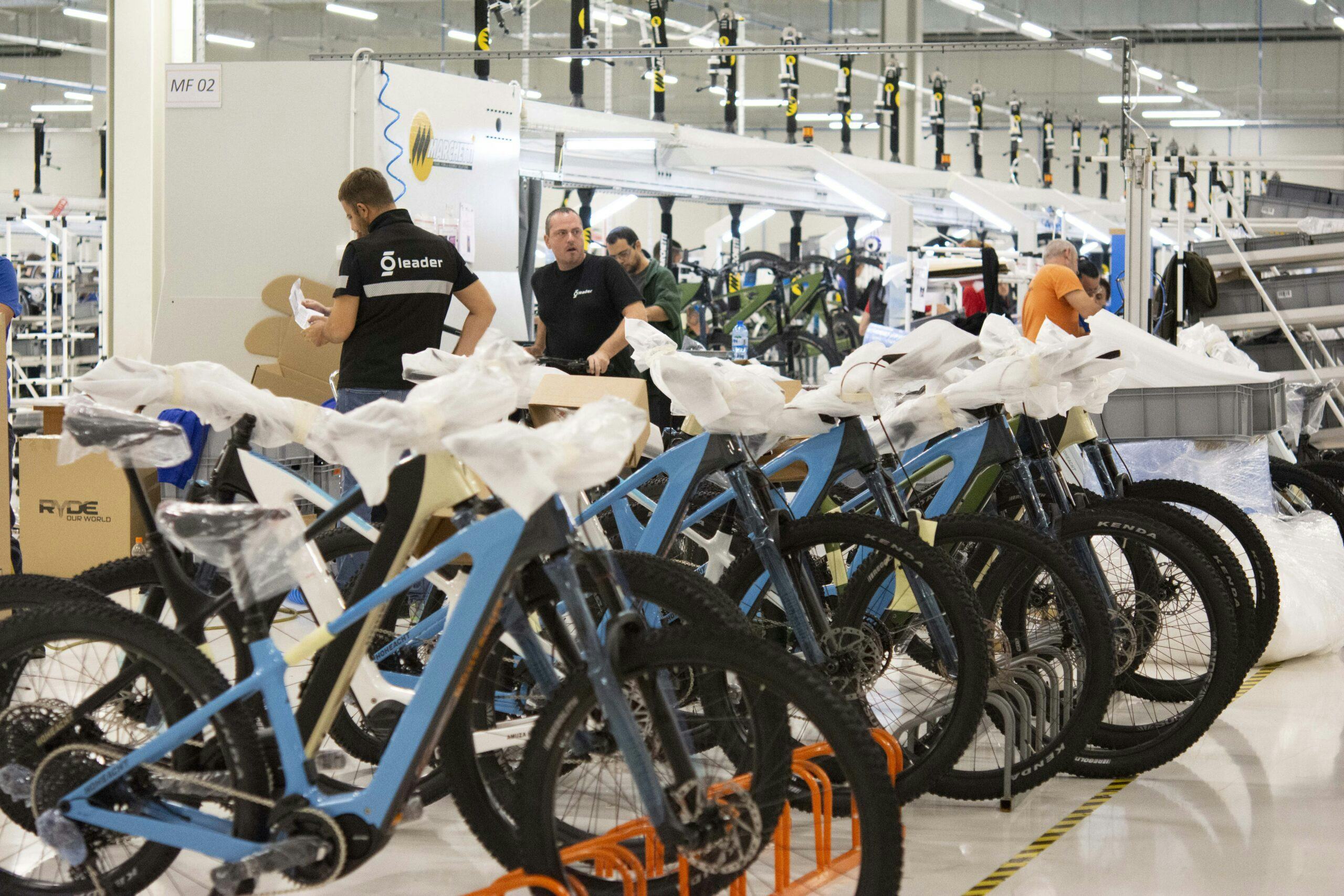
Renowned and respected partner for high-end e-bike projects
Setting ambitious goals for the future and creating a growth roadmap is essential for further development plans. Well-known partners focused on high-end e-bikes already recognised Leader 96 as a renowned and respected company and moved the production of their whole portfolio in the new modern facility. The high-tech factory provides an opportunity to dedicate a production line for specific customer and train the workers according to the highest production standards. With integrated quality monitoring on each step of the flow, agile production process model and an increasing capacity for first class e-bikes models, LEADER sets superior basis offering incomparable service for its OEM partners.
This article is sponsored by Leader 96