DDK’s investment in Vacuum Fitting Technology (VMfit) is part of a bigger investment schema to increase capacity in its production locations in South-East Asia, but also in sustainable production and moving towards Industry 4.0 manufacturing. The production lines with VMfit technology will have an annual output of 5 million saddles.
Sustainable production
“In 2020, we introduced the Rainwater recovery and Waste water disposal system in Vietnam,” explains DDK-Group’s Chief of Sales & Marketing Joy Sung. “We have installed solar panels on the entire roof of the factory in Vietnam. At the same time, we are very pleased to have passed the environmental protection certification of the Vietnamese government in 2021.”
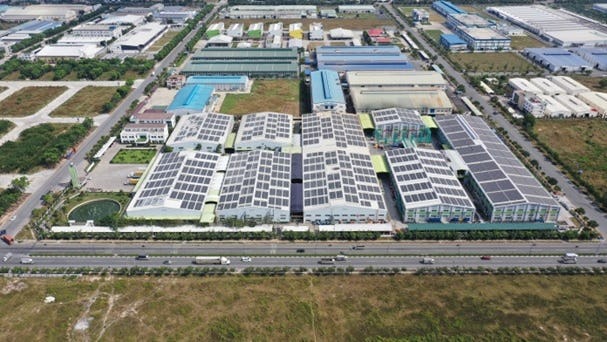
Wide range of technologies
In its factories DDK Group uses a variety of production processes, such as hand-knitting leather, vacuum suction and PU leather. Until recently the company had an annual output of 12 million units. “In order to offer a more diversified manufacturing process and meet the needs of high, medium and low-level customers, we have invested in technology and equipment in the past years. For example we started cross-industry cooperation with well-known shoe suppliers in Vietnam in 2017. We can now add VMfit to our range of production technologies thanks to the R&D investment of more than €7 million,” explains Joy.
“The use of the VMfit technology improves the quality compared to saddles in general. The fully automatic production which does no longer include manual nailing, also allows for all new designs. Hand-made saddles will always encounter design limitations, which can easily be overcome by this new technology. The VMfit saddles are also more water resistant.” Joy notes that shock absorption requirements for e-bike saddles are higher than for regular ones. “The design freedom VMfit offers will also result in saddles which are more capable of meeting those shock absorption requirements.”
Next step in production automation
As early as five years ago DDK Group successively introduced semi-automated and fully automated systems, such as automatic printing and automatic powder coating, automatic injection molding and automatic paper package. However, VMfit technology is a new milestone in the company’s production automation.
“Our current supply is affected by the pandemic in Vietnam,” says Joy. “However, many customers have placed orders with us or changed their orders to VMfit Saddle, which makes us more convinced of our decision to invest in this technology as part of our long term strategy.”
Next factory under development
Next to production in Taiwan and Vietnam, DDK Group is also investing in its subsidiary in Nantong, China. This year, the expected output is already 2 million units. A €3 million investment should increase the capacity to 5 million units annually in 2023.