The production of e-bikes has become increasingly complex in recent years, primarily due to new model variants, new technologies and new legal requirements. In addition to the engine itself, one component in particular poses a significant challenge to the engineers: the battery. From the lithium-ion cells to the battery management system to the housing, everything must be perfectly in tune to ensure the smooth and safe functioning of an e-bike battery. That's why the standards for developing e-bike batteries have also become increasingly complex in recent years.
Certifications or test procedures such as UN 38.3, IEC 62133 or the newly-enacted EN 50604-1 (all standards for lithium batteries) and EN 15194 (requirements for electrically power-assisted cycles) are intended to ensure that no malfunctions, short circuits, and other failures occur during use. "The topic of safety accompanies us in our work every day. In the case of e-bike batteries, functional safety according to ISO 13849, which is derived from the requirements of EN 15194, is particularly important. This includes measures that ensure that a battery functions correctly and that the risk of faults is as low as possible," explains Marcel Wilke, chief technical officer at Akku Vision, a leading e-bike battery producer worldwide.
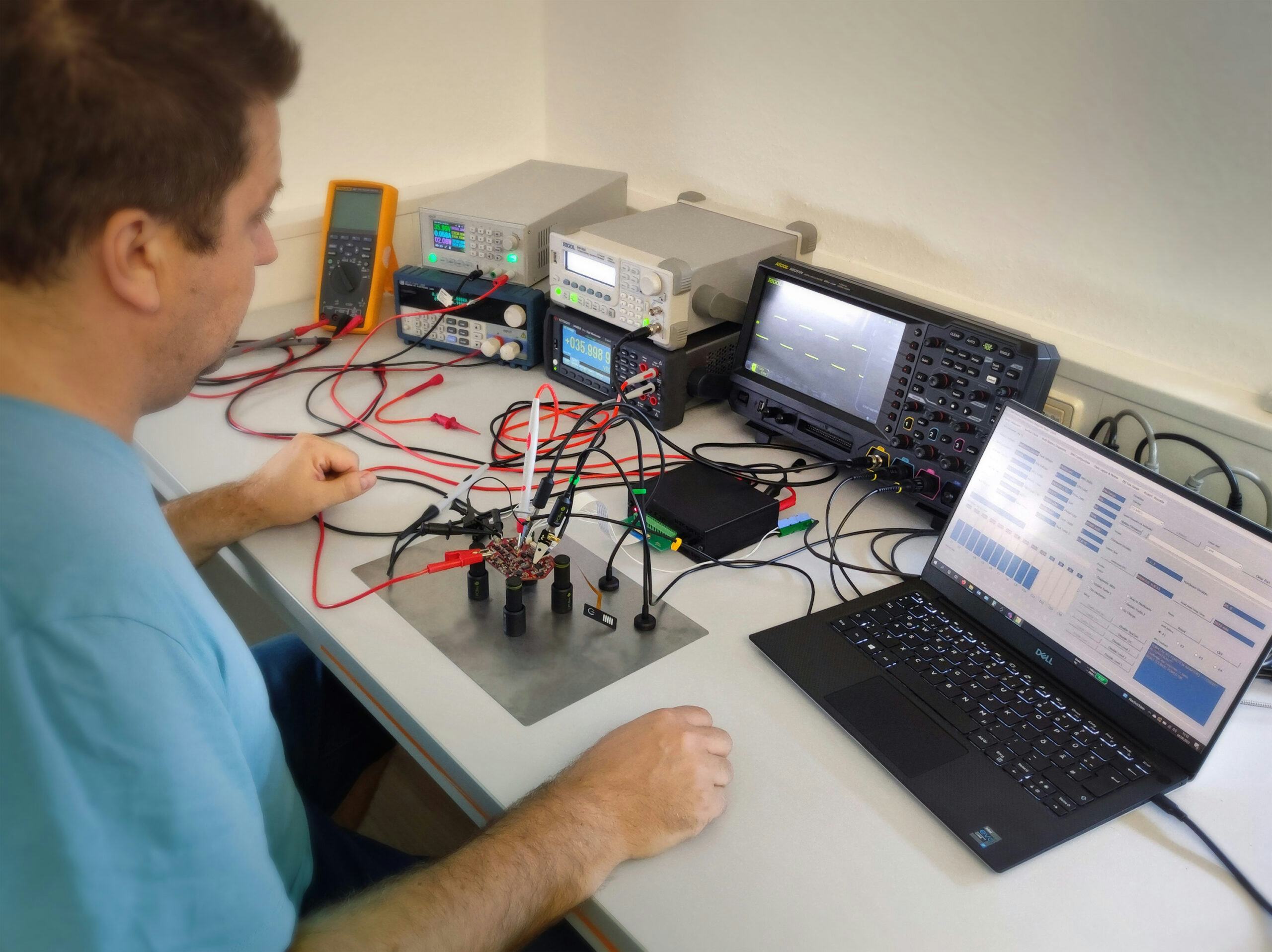
From enquiry to finished product
At its headquarters in Haibach, Akku Vision has been developing and producing e-bike batteries since 2011 for both OEM customers and for the aftermarket. "From requirement analysis to cell selection series production and certification, we offer the full programme from enquiry to finished product," Wilke says. "We develop everything in-house – hardware, software and even most of the testing and inspection equipment come from us. We even have our own test department and also write algorithms ourselves, such as for calculating the charging level of the batteries," he adds.
Our top priority when it comes to the development is safety ”
The German manufacturer places particular emphasis on the functional safety of its products. Elaborate control and test procedures ensure that they not only meet the international standards but even exceed them in many cases – starting with model-specific FMEA (Failure Mode and Effects Analysis) and FMEDA (Failure Modes, Effects, and Diagnostic Analysis) procedures to the calculation of the statistical failure rates of components and circuit parts (MTTFd) to the determination of the performance levels of the protective functions to the battery management system itself.
Exceeding the guideline values
"A standard always represents only the minimum requirement. However, our hardware and software often contain further protective measures that are not required by the standard. However, these additionally implemented measures significantly improve the protection of the battery," Wilke explains.
He also points out that the company's own measures often exceed the guideline values of the international specifications many times over. "Our top priority when it comes to the development is safety. However, the requirements of the standards are often not sufficient to guarantee this in the best possible way. For this reason, we set our own standards. "
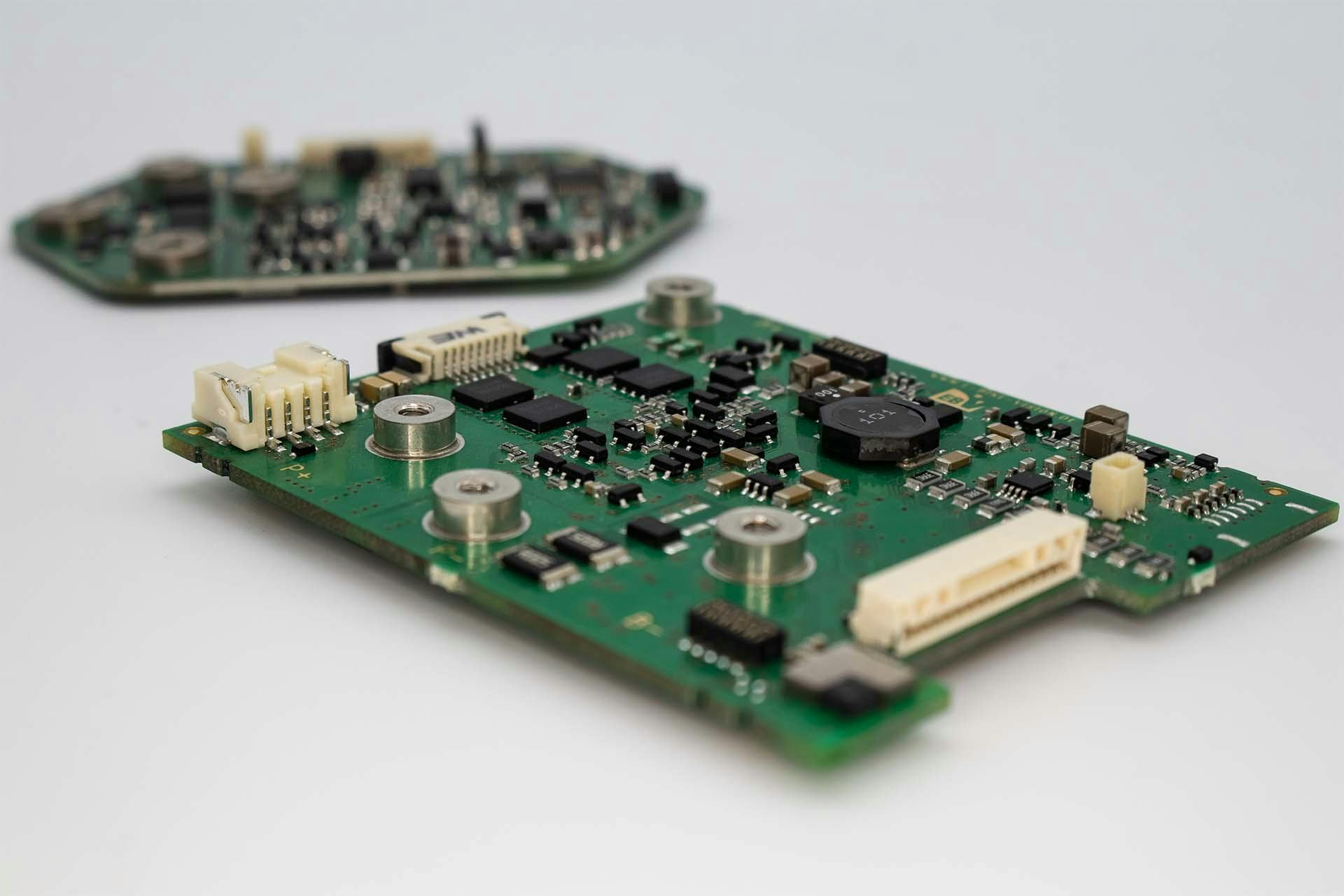
Akku Vision, therefore, protects both the individual cells and the entire battery with multi-level safety systems. These systems monitor, for example, the temperature at several points in the battery pack, the functionality of the battery management system, the charging and discharging current and the individual cell voltage. Another focus is on the protection against a possible overvoltage of cells as well as the prevention of deep discharge.
Additionally, the system should prevent short circuits. This is achieved through specific mechanisms: as soon as a component exceeds previously defined limits, or another problem occurs, the cell pack is switched off by a protective function. "Depending on the requirements, five to ten of our engineers are involved in developing a battery. Due to the high requirements and the equally high demand for our products, we need about six to twelve months to develop and test a new product," Wilke reports.
High internal standards for international success
Wilke is particularly proud that all development and production steps take place in the company's own factory. Only training and product certifications are sometimes outsourced. For example, six employees were recently trained by TÜV SGS Saar to become certified Machinery Functional Safety Professionals (MFSP). Currently, there are only 75 such experts in Germany.

"So we provide almost 10% of them," says Wilke. Because of this accumulated know-how in his own company, the Akku Vision CTO is more than optimistic about the future. This is all the more true as the standards for e-bike batteries will continue to become more complex in the coming years – possibly at the same speed as the rapidly increasing sales figures of pedelecs worldwide.
This article is sponsored by Akku Vision.