“Our annual sustainability report reveals a notable trend: our carbon intensity is getting smaller and smaller. In 2022 we passed a significant milestone, reducing our Scope 1 and 2 emissions to zero. We are probably one of the very first in the bike industry to reach this goal, and we’ve also reduced our Scope 3 emissions by 16%”, says Sari Noromies, Operational Excellence & Sustainability Developer.
Renewable energy since 2017
Herrmans uses the GHG Protocol to measure its emissions. With careful management, Scope 2 emissions have long been under control (scope 2 includes indirect emissions from the production of purchased energy). A key to achieving this reduction is that Herrmans has for many years been using 100% renewable energy - 50% hydro power and 50% wind power for its offices and manufacturing plant in Finland.

Electrifying the vehicle fleet
"Replacing the factory’s diesel-powered vehicles and forklifts with electric alternatives contributed to the latest achievement of zero Scope 1 emissions," Sari Noromies states. "The first electric trucks are already in use, and the remaining vehicles will gradually be replaced with electric ones. The small quantity of remaining emissions is offset by our support of rainforest projects in Borneo."
Nucore
The latest addition to Herrmans’ portfolio is the bio-based bicycle grip series Nucore. One of Herrmans main goals is to gradually decrease the dependence on fossil-based plastics, which is a pre-requisite to becoming fully carbon neutral in all 3 scopes by 2035. The biobased materials are made with renewable resources such as plants and vegetable crops for industrial use, grown on soil that is not fit for food production.
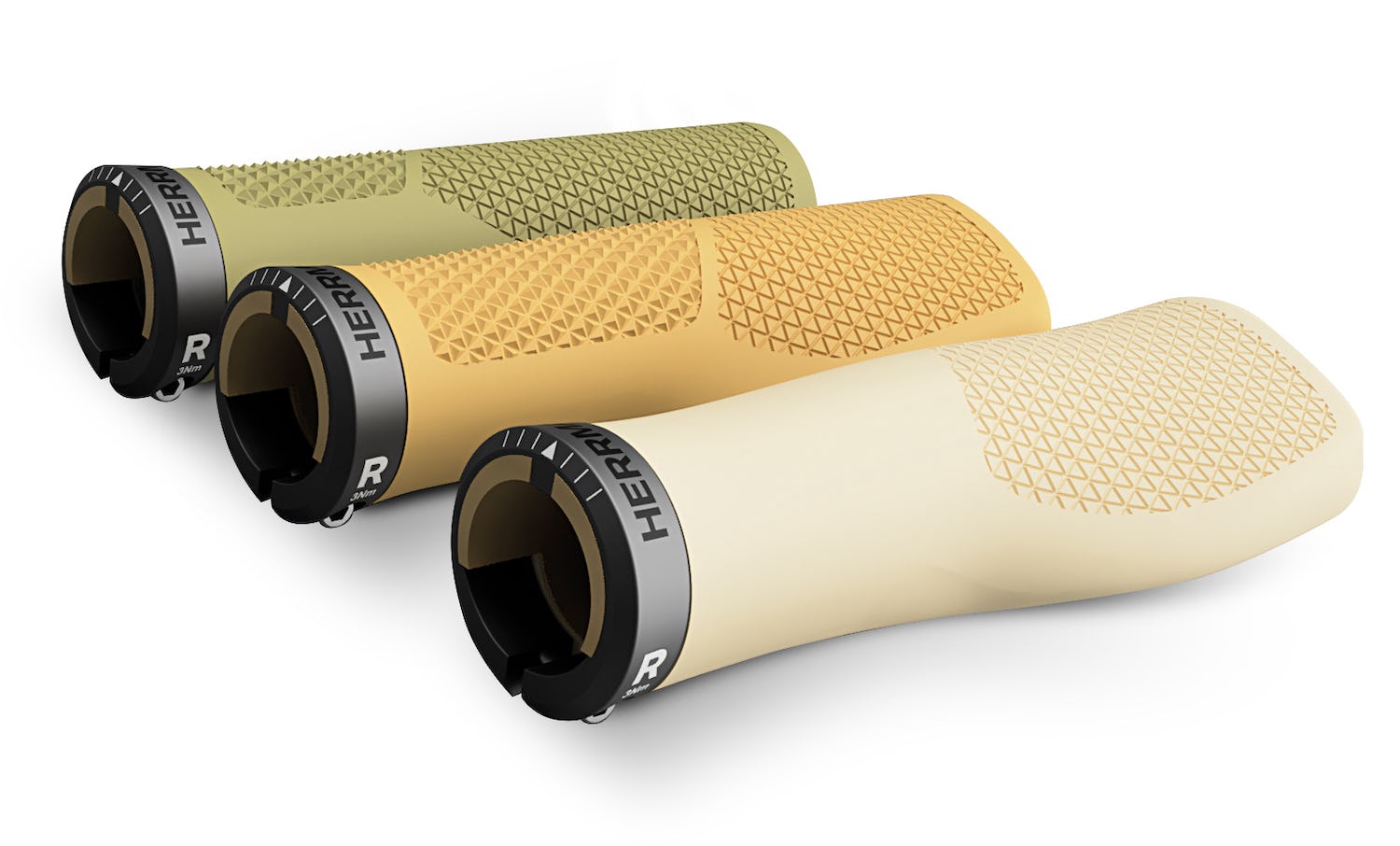
“Bio-based material use is one of the ways we futureproof our product portfolio, and we will gradually increase the ratio of bio-based vs regular plastic, as we learn more about how to use them in serial production and injection molding, and as new materials come out on the market. The demand and interest is high for these materials, so the development is rapid and we are evaluating all options as they become available,” says Sari Noromies.
Recycled materials a parallel road
A chain guard, spoke protector and various components made from 100% recycled materials are already on the market. Herrmans is also improving the ways in which production waste is used: "The very best way to be more sustainable is to reuse any waste from production immediately with the help of grinders, that grind and feed the waste directly back into the machine,” says Sari Noromies.

Product scoring for easier comparisons
Concurrently, Herrmans is developing a product scoring system to better analyze material flows and remain at the forefront of pioneering industry standards. “It is no longer sufficient to say that our products are superior or more sustainable; we must support such claims with facts,” says Sari Noromies. Herrmans is working on a way to explain how much of an impact a certain product has – be it materials, lifetime expectancy, transport distance etc – all important contributors that should be factored in, when a bike manufacturer or end consumer makes an informed decision to compare how sustainable a certain component is at a certain price.
CEO Dan Liljeqvist is also pleased with the company’s development: “Although this is a long-term commitment, we are now starting to get tangible results from our efforts as momentum is growing in the organization. This is mainly due to the gradual increase in products made from recycled materials. Our sustainability efforts are also about cultivating our reputation as an attractive business partner and employer, and about attracting skilled employees. What’s also rewarding is knowing that our choices help the world become a slightly better place. The goal is to help bike manufacturers to produce more sustainable bikes and make it possible for end consumers to make a conscious choice when they buy new parts for their bikes.”
For Herrmans, sustainability is a fundamental principle, embedded in its strategy, business plans as well as in the organizational culture. Today, 10% of its products are manufactured using recycled materials, and this is only the beginning. The company has set itself the ambitious target of achieving carbon neutrality across its operations by 2035. Herrmans’ sustainability strategy has three pillars: people, profit, and planet. It seeks to strike a balance between all three.
This article is sponsored by Herrmans Bike Components.